Customized Solutions - Our Core Competence
Unlock Production Potential
During its service life, every grinder must be regularly reassessed in terms of quality, productivity, and efficiency. As the life cycle of the machine progresses, operational wear reduces machine availability and unplanned repairs significantly increase maintenance costs. The supply of spare parts, especially with regard to the electrical system, can no longer be guaranteed due to obsolete components and the profitability of the machine is progressively reduced due to outdated technologies and obsolete production conditions.
How must an existing machine be modified so that roll machining can be carried out as efficiently and profitably as possible? What measures are necessary to ensure consistent quality and compliance with current safety standards?
Modernization with Concept
With over 30 years of experience and in close cooperation with our customers, we develop individual modernization concepts based on in-depth analyses of your existing roll grinder.
Grinding technology, mechanical equipment, media technology, electrical systems, control systems, quality assurance and their complex interactions are considered as a whole and aspects such as safety requirements and customer-specific standards are also taken into account.
The result is a future-orientated and cost-effective solution for all your projects, regardless of the required technological expansion stage. Thanks to forward-looking modernization concepts, we achieve an optimum return on your investment, reduce downtime during modernization to a minimum, and ensure fast start-up.
Our Services
For the modernization of roll grinding machines, a distinction is made between several variants and expansion stages.
Thanks to our qualified employees and as part of the HerkulesGroup, we have in-depth expertise in all disciplines.
Starting with the replacement of individual components or entire assemblies, delivery including integration of additional units through to the complete redesign of the machine.
Analysis and Transparent Advice Before Modernization
- Detailed assessment and documentation of the actual condition of the grinding machine
- Comprehensive analysis of the machine with regard to its weaknesses and activation of possible potentials
- Collaborative objective definition based on customer-specific requirements, expectations, and desired end results
- Development of a well-founded solution concept to guarantee the customer's defined long-term goals
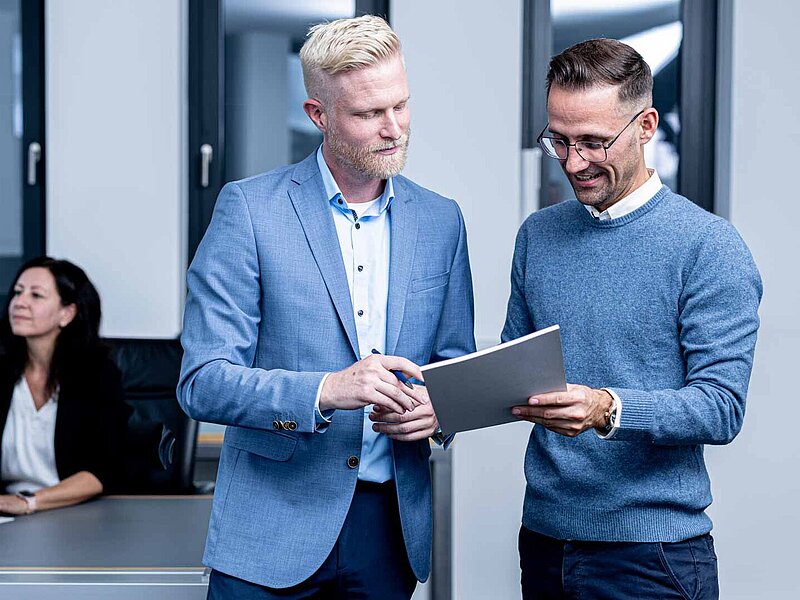
Modernization of the Mechanical Equipment
- Retrofitting of high-performance grinding heads (X-axis) in composite design with mineral cast body
- Conversion of complete feed axes to modern drive systems
- Modification / improvement of lubrication systems - Replacement of guideway coatings
- Optimization of the machine structure - Rigidity optimization and improved vibration damping
- Overhaul / renewal of hydraulic and pneumatic units
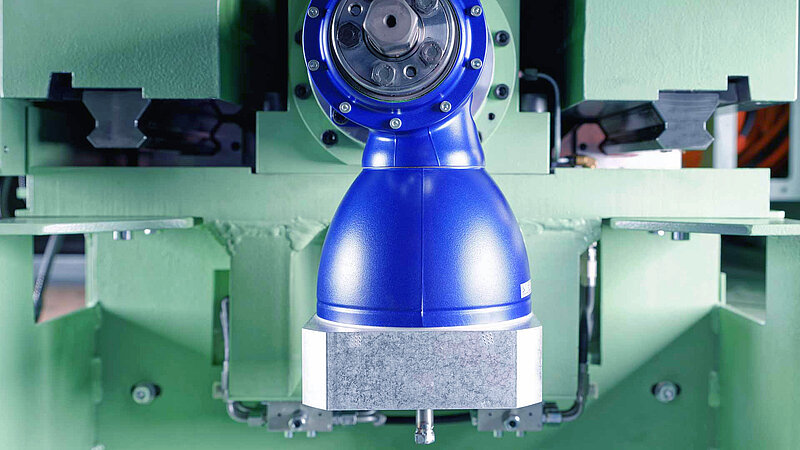
Modernization of the Electrical System
- Complete control cabinet engineering including machine cabling and redesign of the energy supply system
- Project planning and replacement of electric motors and converters
- Investment security through the use of high-performance components with long-term availability from renowned manufacturers
- Installation of smart sensors for precise data acquisition and data analysis
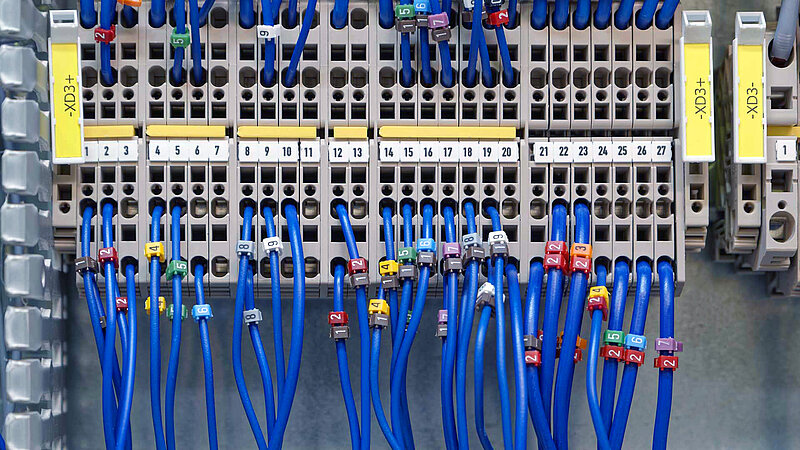
Upgrade of the Control Technology
- Installation and initial start-up of the state-of-the-art KP10 grinding machine control system
- Design of intuitive and ergonomic operating concepts
- Roll shop management systems - comprehensive integrated tools for complete roll shop management
- Industry 4.0 ready - thanks to modular and future-orientated technologies (IoT)
- Mechatronic solutions for diagnostics, data analysis and condition monitoring for maximum transparency in the grinding process
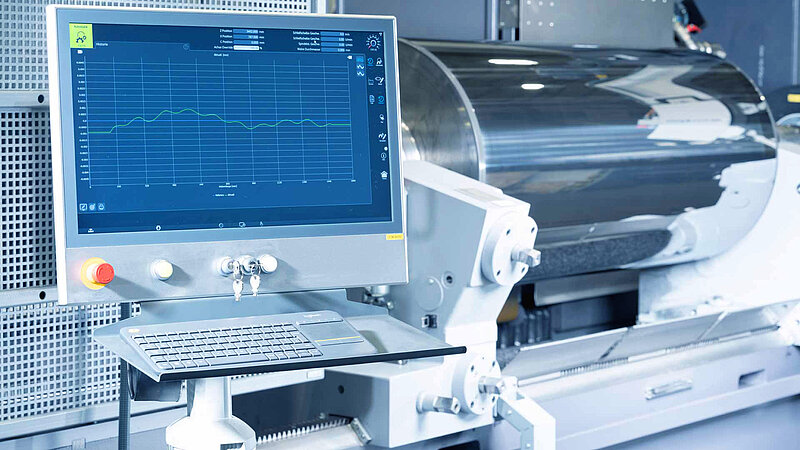
Upgrade of the Roll Measuring Systems incl. Inspection Systems
- Fully integrated stationary roll measuring systems for the steel industry - “on the fly”
- Fully integrated stationary roll measuring systems for the paper industry - for roll diameters up to 3,000 mm incl. height measurement
- Seamless quality assurance using high-resolution roll inspection systems - integrated or as stand-alone systems
- Innovative surface measurement technology for optimum rolling mill performance - integrated or as stand-alone systems
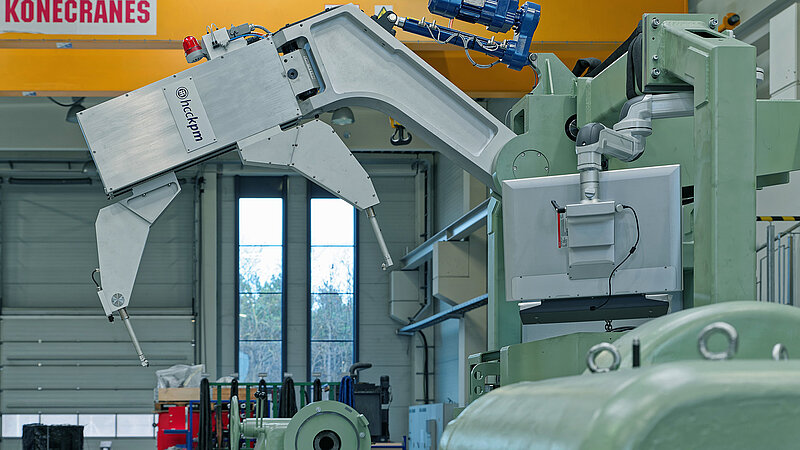
Retrofitting Safety Technology
- Performance of legally compliant risk and hazard analyses in accordance with current standards and customer-specific requirements
- Planning and implementation of pragmatic safety concepts, taking into account practical aspects
- Hazard prevention and risk minimization for increased employee protection and machine safety
- Complete integration into the grinding machine control system
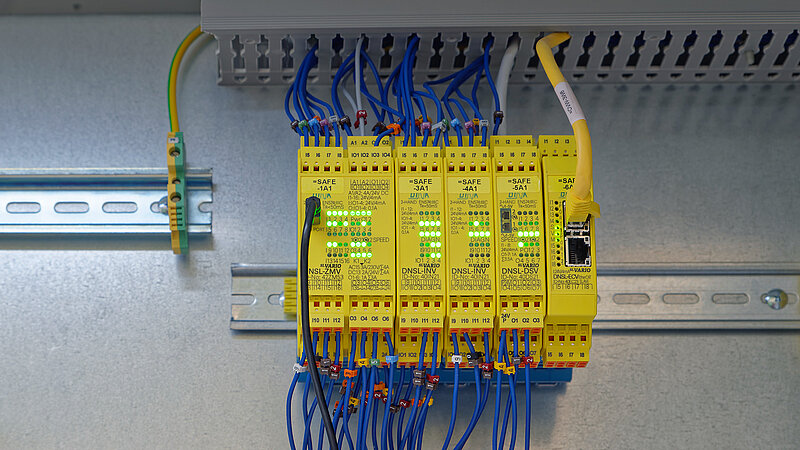
Holistic Modernization – SBA Innovations
- Backlash-free drive and guideway systems for all machine axes: Linear guides for the Z and X axes
- CBN-ready thanks to the installation of high-end motor spindles: 120 m/s circumferential speed of the grinding wheel
- Comprehensive automation solutions to reduce set-up and downtimes: Fully automated roll loading and alignment
- B-axis technology for optimum contour grinding: Development of the solid-state bearing (swivel axis for the grinding wheel)
- Machine extensions
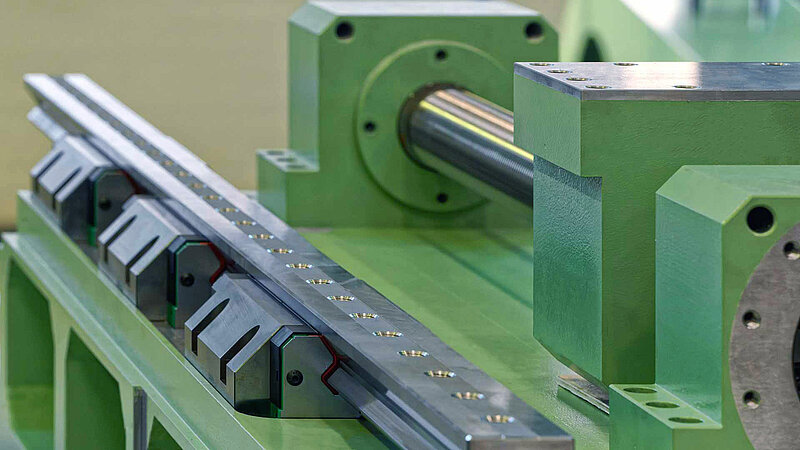